Understanding What is Porosity in Welding: Reasons and Solutions
Wiki Article
The Scientific Research Behind Porosity: A Comprehensive Guide for Welders and Fabricators
Recognizing the elaborate devices behind porosity in welding is important for welders and fabricators pursuing remarkable workmanship. As metalworkers look into the depths of this sensation, they reveal a world controlled by various aspects that affect the development of these small spaces within welds. From the make-up of the base products to the ins and outs of the welding procedure itself, a plethora of variables conspire to either worsen or alleviate the visibility of porosity. In this comprehensive guide, we will untangle the scientific research behind porosity, discovering its results on weld high quality and unveiling progressed techniques for its control. Join us on this trip through the microcosm of welding flaws, where precision meets understanding in the search of flawless welds.Recognizing Porosity in Welding
FIRST SENTENCE:
Exam of porosity in welding exposes critical insights into the stability and quality of the weld joint. Porosity, characterized by the visibility of dental caries or gaps within the weld metal, is an usual problem in welding processes. These gaps, if not appropriately dealt with, can jeopardize the architectural integrity and mechanical properties of the weld, causing possible failings in the ended up item.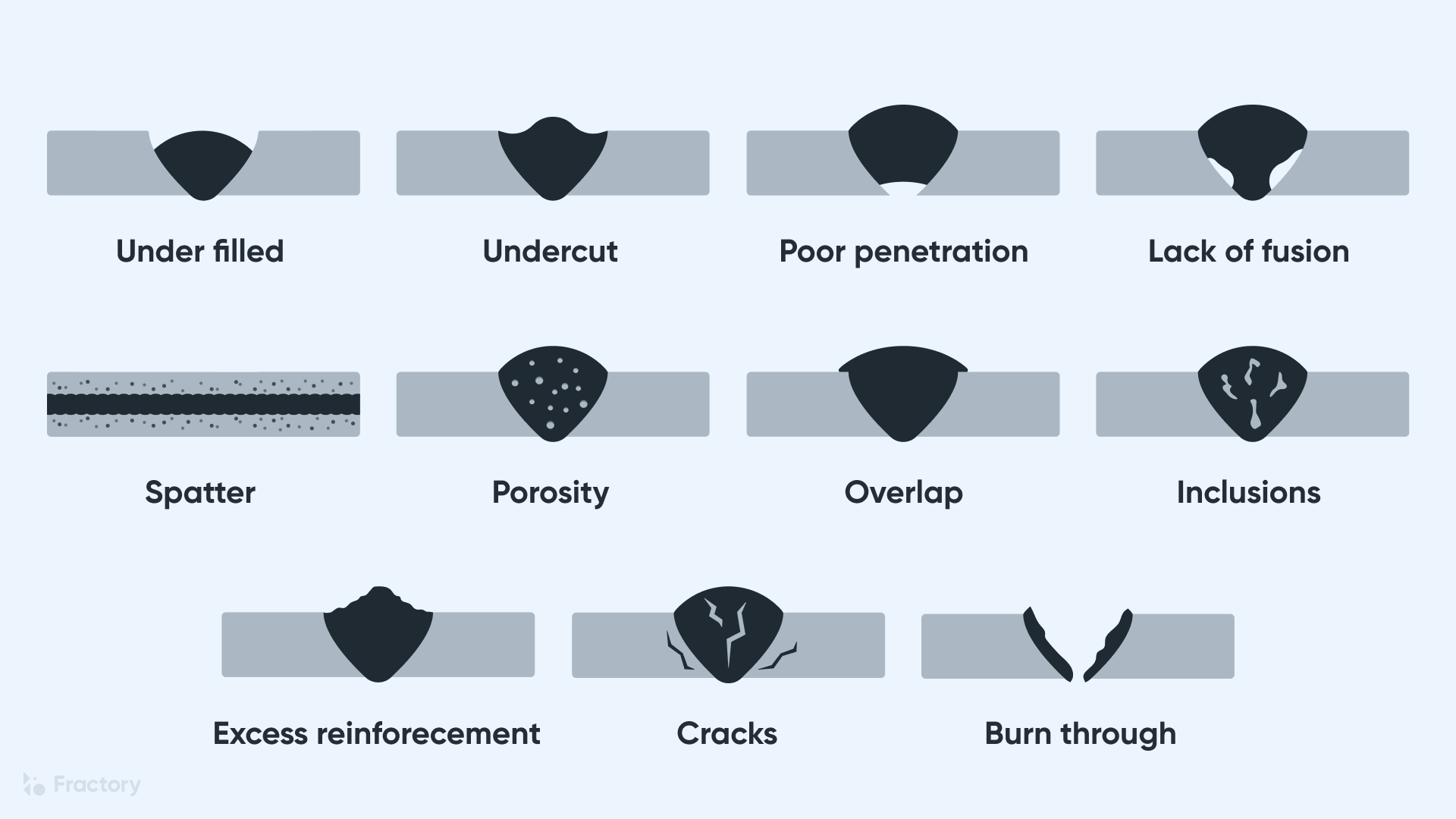
To discover and evaluate porosity, non-destructive screening approaches such as ultrasonic testing or X-ray inspection are commonly used. These strategies enable the identification of internal problems without jeopardizing the stability of the weld. By assessing the dimension, form, and circulation of porosity within a weld, welders can make enlightened choices to boost their welding processes and accomplish sounder weld joints.

Factors Influencing Porosity Formation
The event of porosity in welding is affected by a myriad of aspects, varying from gas securing performance to the complexities of welding specification setups. Welding specifications, consisting of voltage, current, take a trip speed, and electrode kind, additionally impact porosity development. The welding strategy utilized, such as gas steel arc welding (GMAW) or shielded metal arc welding (SMAW), can influence porosity formation due to variations in warmth distribution and gas insurance coverage - What is Porosity.Effects of Porosity on Weld High Quality
Porosity development substantially compromises the architectural honesty and mechanical properties of welded joints. When porosity exists in a weld, it creates spaces or tooth cavities within the material, minimizing the total toughness of the joint. These spaces work as stress concentration points, making the weld a lot more at risk to cracking and failure under tons. The visibility of porosity additionally weakens the weld's resistance to corrosion, as the caught air or gases within the gaps can respond with the surrounding environment, resulting in deterioration gradually. In addition, porosity can prevent the weld's capability to stand up to stress or influence, more threatening the total top quality and integrity of the bonded framework. In essential applications such as aerospace, auto, or architectural constructions, where safety and resilience are paramount, the destructive results of porosity on weld top quality can have extreme effects, stressing the value of lessening porosity through proper welding techniques and treatments.Methods to Minimize Porosity
To boost the quality of bonded joints and ensure architectural honesty, welders and producers employ certain techniques focused on reducing the formation of voids and dental caries within the material during the welding procedure. One effective approach to reduce porosity is to ensure appropriate material prep work. This includes thorough cleaning of the base steel to get rid of any type of impurities such as oil, oil, or moisture that might add to porosity formation. Furthermore, making use of the suitable welding specifications, such as the appropriate voltage, existing, and travel speed, is vital in avoiding porosity. Keeping a regular arc length and angle during welding also helps in reducing the likelihood of porosity.
Additionally, choosing the ideal protecting gas and preserving appropriate gas flow rates are necessary in minimizing porosity. Using the appropriate welding technique, such as back-stepping or using a weaving movement, can additionally assist distribute heat evenly and lower the chances of porosity development. Finally, making certain correct air flow useful link in the welding atmosphere to eliminate any type of potential resources of contamination is essential news for attaining porosity-free welds. By applying these strategies, welders can successfully lessen porosity and create high-grade bonded joints.

Advanced Solutions for Porosity Control
Implementing sophisticated innovations and innovative approaches plays an essential function in achieving superior control over porosity in welding processes. One innovative option is making use of advanced gas combinations. Protecting gases like helium or a mix of argon and hydrogen can aid decrease porosity by offering better arc security and improved gas insurance coverage. Additionally, using advanced welding strategies such as pulsed MIG welding or modified environment welding can also assist mitigate porosity problems.One more sophisticated remedy involves making use of sophisticated welding tools. Using equipment with integrated features like waveform control and sophisticated power sources can enhance weld high quality and minimize porosity threats. In addition, the application of automated welding systems with precise control over parameters can dramatically decrease porosity issues.
Additionally, integrating sophisticated monitoring and evaluation innovations such as real-time X-ray imaging or automated ultrasonic testing can help in finding porosity early in the welding procedure, permitting instant corrective actions. In general, integrating these innovative remedies can useful source substantially boost porosity control and improve the general quality of bonded elements.
Final Thought
In final thought, understanding the scientific research behind porosity in welding is essential for welders and producers to produce top quality welds - What is Porosity. Advanced solutions for porosity control can better improve the welding procedure and guarantee a solid and reputable weld.Report this wiki page